Coal Mine Fires and Burning Refuse
Caveat: Coal mine fires or underground mine fires are generic terms for coal seam fires. The reason the “mine” is used within the description is due to the starting point of the fire. The majority of coal seam fires start within active or abandoned coal mines. It is important to note that the mine itself is not on fire, but the remaining coal pillars, remaining coal seam, poor quality coal, or burnable debris left behind is what burns.
Mine Fires: Majority of mine fires start through careless human activity, such as burning debris within an abandoned surface mine; however, mine fires can also start naturally via forest fires, lightning strikes, lava flows or other natural heat sources.
Underground coal mine fires occur around the world, sending thousands of tons of soot, toxic vapors, and greenhouse gases into the atmosphere, leading to pollution of surface and groundwater, mine subsidence as the coal is consumed, and ignition of forest and structural fires. Areas like the resort town of Glenwood Springs, Colorado has been plagued by series of suspected mine fire caused forest fires which burned thousands of acres of forest and many local residences.
Underground Mine Fire Thermal Cycle
When the fire travels into the ground from the surface it creates a thermal cycle. The thermal cycle consists of the fire heating the air causing it to rise and escape through passageways (fractures) in the ground. The points on the ground surface where the heated air discharges into the atmosphere are known as vents. The heated air carries the greenhouse gases, noxious fumes, soot, and smoke. These vents are extremely dangerous and pose a serious health risk. Vents encountered or discovered need to be avoided, never get closer than 100 feet to a vent.
With the hot gases rapidly venting, this creates a negative pressure at the fire face. Cooler, oxygenated air drawn from the outside atmosphere is pulled into the ground and ultimately to the fire, thus completing the thermal cycle. As the fire spreads into the coal seam new vents can form and old vents can change becoming intake vents.
Eastern Kentucky Mine Fire. The smoke is coming from underground haulage ways, exposed by surface mining. (SOURCE: Geology of Coal Fires: Case Studies from Around the World, The Geological Society of America.
According to e-AMLIS, in 2013 there were 98 underground mine fires in 9 states. This is considered to be an underestimate for the actual number of fires nationwide.
Coal mining states programs address mine fire and coal refuse fire related emergencies. These fire emergencies can threaten to ignite forest fires and underground mines fires that can burn beneath buildings, roadways and grounds releasing deadly gases and causing mine subsidence. Abatement methods range from complete excavation and quenching with water, to the use of specialty foaming cements and firefighting foams that are injected into the fire through boreholes drilled from the ground surface. Other techniques that may be used include the use of liquid nitrogen to extinguish the fire by the rapid removal of heat.
Warning Sign from Centralia, PA
For information regarding this webpage and Mine Fires please contact:
Frequently Asked Questions
Types of mine fires:
- Burning coal seam: This type of underground fire follows the fuel source (carbon) along the coal seam. Based on geological structure, these fires break into two categories:
- Horizontal coal beds
- Coal seams which are generally flat lying. Occurrences are generally east of the Rockies and in Northern Alaska. Fires within these coal beds are typically easier to characterize and delineate.
- Angular beds
- These coal seams follow geologic structures such as anticlines and synclines. The angle degree can be up to 90 degrees. These type of coal seams occur within the Rocky Mountain and Southern Alaskan Ranges as well as the anthracite fields of Eastern Pennsylvania. Due to the angled bedrock, characterization and delineation of these fires can be difficult.
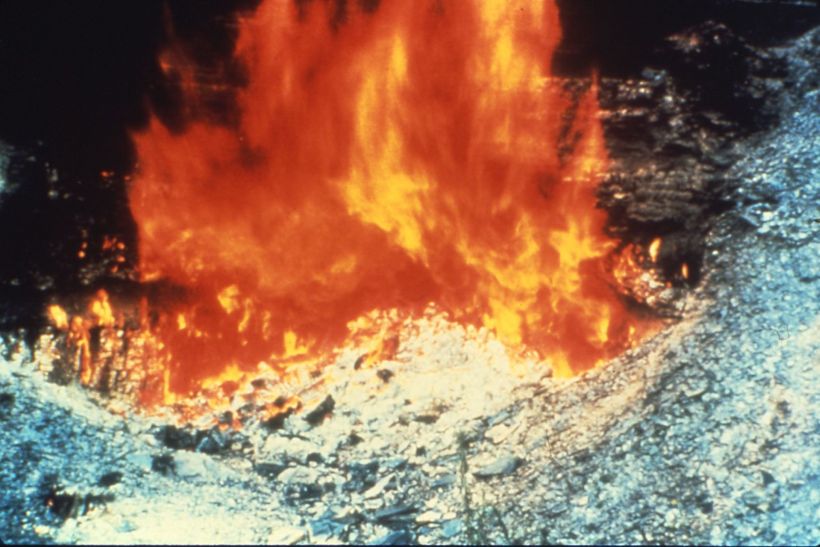
- Burning Refuse: These fires occur within coal waste piles or culm piles. Not confined to a singular seam, this fire type will burn from the ignition point spreading out into the pile. The difficulty in extinguishing these fires is due to the size of these piles. These piles can range in size from an acre to hundreds of acres, with the largest being 1.5 miles in length.
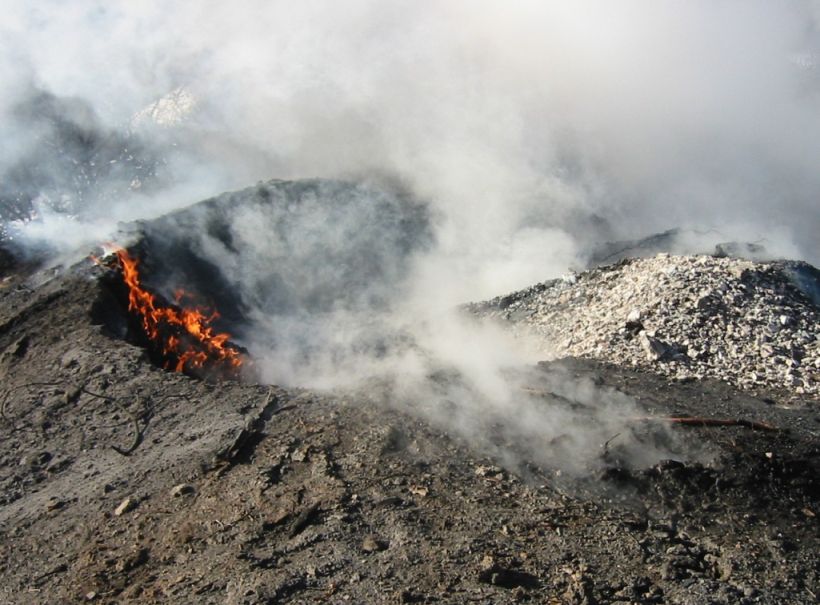
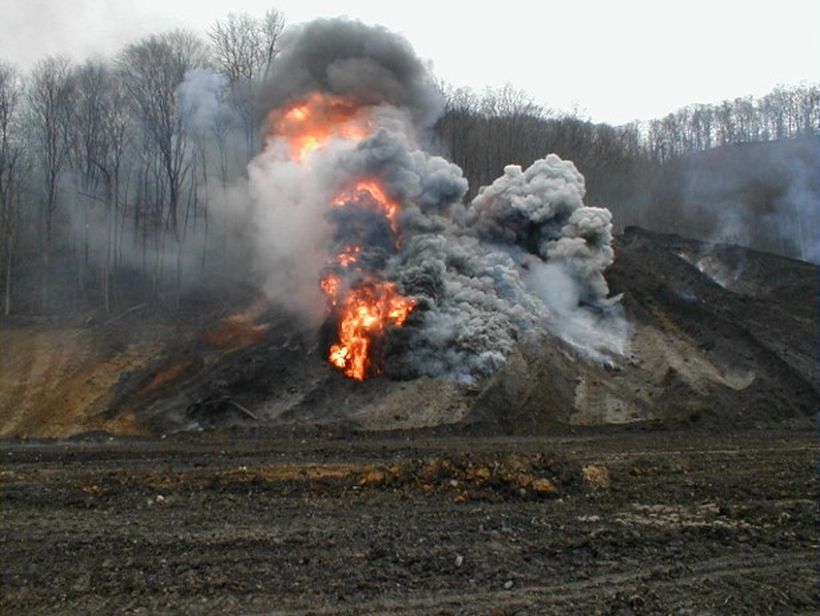
Mine fires or coal seam fires are Class “A” fires according to the U.S. Fire Administration. Class “A” fires burn materials such as wood, paper, cloth all of which leaves ashes. Common extinguishing methods for Class “A” fires is the use water or foam to cool or smother the fire.
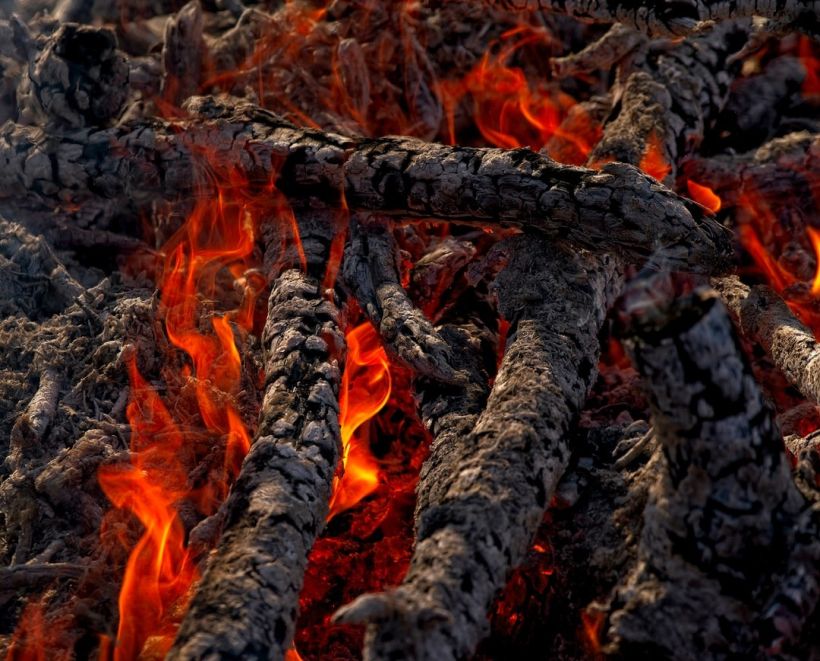
A mine fire can also at times be a Class “B” fire when pockets of methane are encountered. This would cause a flash or fire ball which may burn for several minutes to several hours dependent on the amount of available methane. Fortunately, these Class “B” fires occur underground and would not be noticeable above the ground surface.
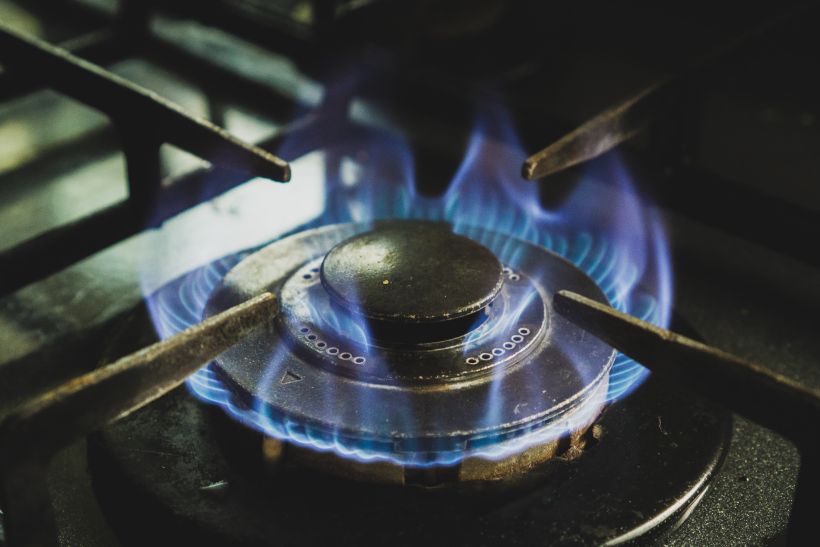
The ignition temperature for coal is dependent on the type of coal and its moisture content. The temperatures listed below are rough average temperatures of the types of coal as compared to wood.
Wood –572° F (300°C) Sustained burn 1472 to 1742°F (800 to 950°C)
Lignite – 525° F (274° C)
Sub-Bituminous – 662° F (350° C)
Bituminous Coal – 700° F (371° C)
Sub-Anthracite – 752° F (400° C)
Anthracite Coal – 1,700° F (927° C)
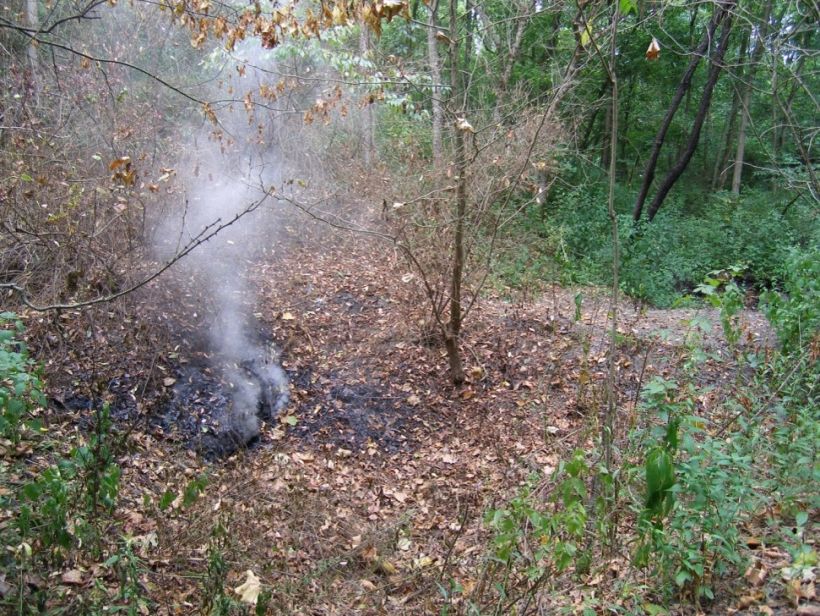
First of all, stay clear of the vent.
If the smoke or vent is near/entering a building or is in danger of causing personal or property damage, call 911.
If you discover a vent where there is not an immediate health or fire risk, contact your states abandoned mine lands office and notify them of your discovery.
When notifying your state via phone or email, please include or have ready the following information:
- Your name and telephone number
- Location of event or closest crossroads
- County and township or municipality
- And a description of the issue
- If able, provide picture(s) of the danger
There are many factors which can dictate how a mine fire is extinguished.
• Size of the fire area.
• The depth of the coal seam.
• Location of the fire within the coal seam and mined areas. Important to determine potential pathways the fire may progress.
• The length of time the fire has been burning.
• Local geology.
• The presence of methane, and
• A few others
Like all fires, the faster the response time the greater the chances of extinguishing it with minimal costs and environmental damages.
Remembering back to the fire triangle (below); a fire can only be extinguished by removal of one of the legs of the triangle. As the figure below shows, for coal to burn it must have a temperature of 150 degrees Fahrenheit, greater than three percent oxygen (21% in the air we breathe), and >20% carbon in the coal. Removal of any one of these items will result in the fire extinguishing.
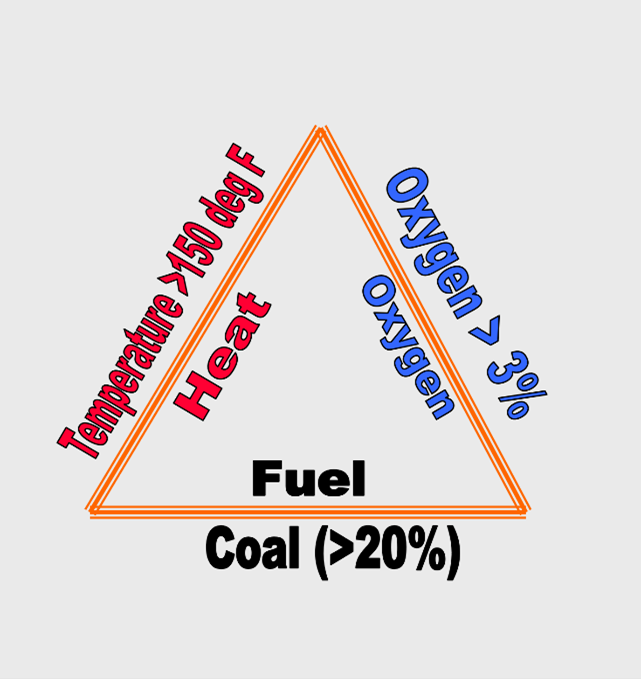
There are three basic types of extinguishment concepts.
- Isolation – This concept attempts to remove or reduce the available fuel supply (coal) to the fire thereby eliminating the fuel portion of the fire triangle. Included within this concept is hazard removal from the fire areas.
- Encapsulation – This concept involves covering the fire indirectly with a medium which will limit or prevent the flow of oxygen from reaching the fire.
- Injection – This involves injecting flowable solutions into the mine voids at or near the fire location to remove the heat or prevent oxygen from reaching the fire.
Fire Isolation Concept
There are several common practices which use the isolation concept to fight mine-fires. They include:
- No Action
- Relocation/Removal
- Trenching
- Impassible Barriers Walls
- Injected Barrier Walls
- Cutoff Walls
In all cases, the objective is to decrease the impacts of the fire on the public/environment or reduce the available fuel source for the fire.
“No Action” Application:
This application does not involve any remedial action. The fire is left alone to burn unabated.
Overall Effectiveness: Not effective. Fire and associated hazards remain and will continue until fuel is exhausted.
Environmental Impact: High potential for environmental and public impacts. Mine fires left to burn unabated have the increased risk of igniting forest fires/grasslands, formation of new subsidence features, vents, and intakes, as well as expulsion of gasses and soot into the atmosphere.
Relative Costs: Since the fire is not being fought, the associated costs are negligible. However, costs associated with the risks of leaving the fire alone can be quite high.
Worker Safety: Not Applicable.
Public Safety: Public safety risks are high due to hazards mentioned above.
Depth of Fire: Not Applicable.
Multiple Burning Seams: Not Applicable.
Available Technology: Not Applicable.
Treatment Time: None.
Structural Geology: Not a concern.
Gasses, Smoke, and Soot: The risk of gasses, smoke and soot is high due to the lack of intervention.
Treatment by-products: None.
Maintenance and Monitoring Costs: None.
Relocation/Removal Application
This application involves the removal of the public from the dangers of the mine fire. Centralia, Columbia County, PA is an example of where this was used. Monies are made available to affected residences, businesses, and utilities for relocation outside of the fire area. After this is accomplished, the fire is monitored and left to burn. As in the case of Centralia, the fire has been burning more than 50 years.
This application is used when the cost of extinguishing the fire is more than the costs of relocating affected residences.
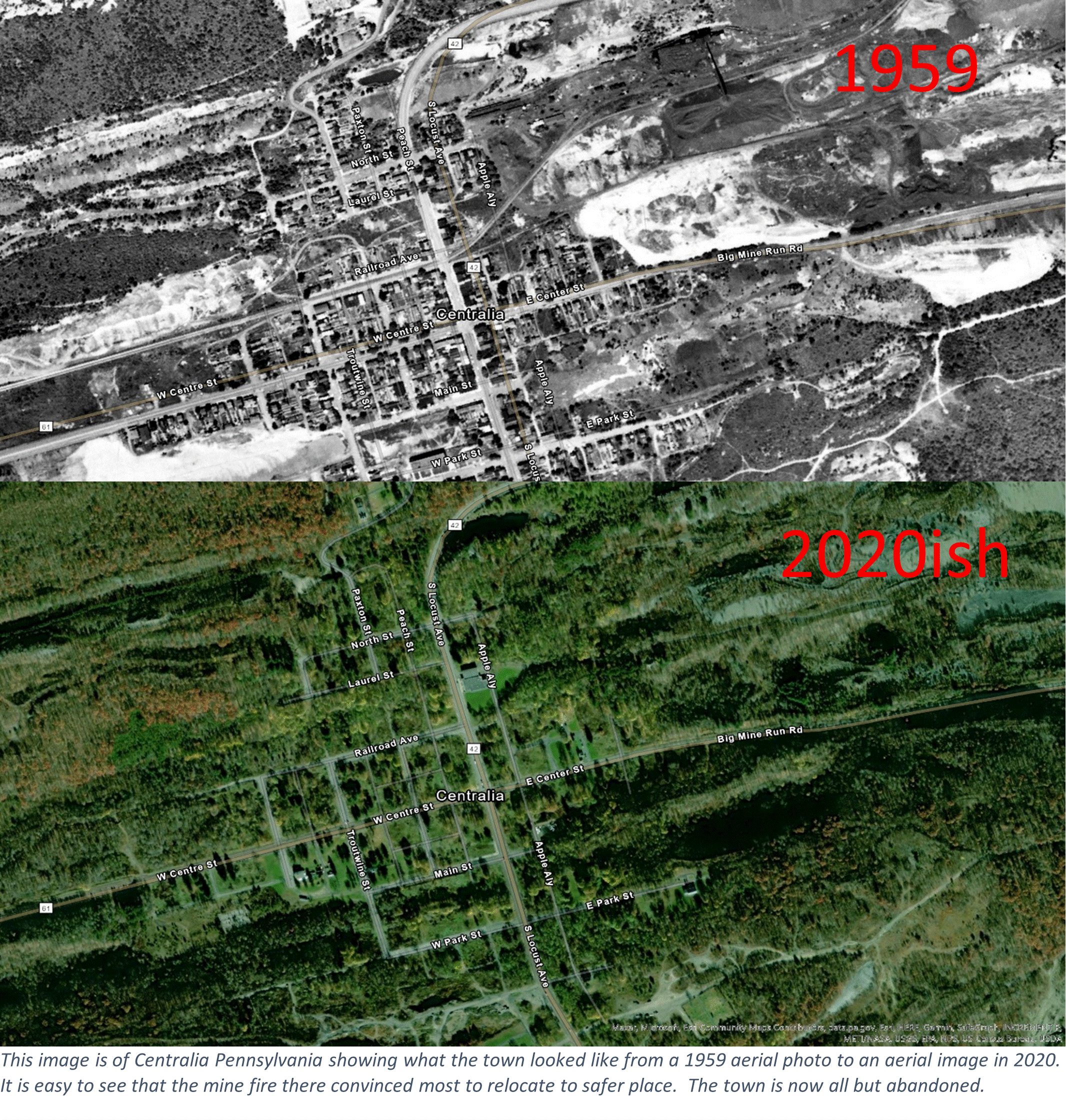
Analysis of “Relocation/Removal Application:”
Overall Effectiveness: Effective in removing public interactions with the fire zone. Environmental impacts remain present.
Environmental Impact: High potential for environmental impacts. Mine fires left to burn unabated have the increased risk of igniting forest fires/grasslands, formation of new subsidence features, formation of new vents and intakes, as well as expulsion of gasses and soot into the atmosphere.
Relative Costs: Costs associated with the removal/relocation of private, public, and business structures can be very costly. Furthermore, as the fire continues to burn, the likelihood that new properties will become effected and require relocation.
Worker Safety: There is a minor to moderate risk to workers as properties are purchased and demolished. Mine fire gasses may be present in abandoned structures requiring special monitoring and personal protective equipment (PPE).
Public Safety: Public safety risks are eliminated for parties who relocate. Individuals who choose to remain and spectators/trespassers onto mine fire lands continue to have elevated safety risks.
Depth of Fire: Not Applicable.
Multiple Burning Seams: Not Applicable.
Available Technology: No technologies required.
Treatment Time: None.
Structural Geology: Not a concern.
Gasses, Smoke, and Soot: The risk of gasses, smoke and soot is high due to the lack of intervention.
Treatment by-products: None.
Maintenance and Monitoring Costs: Costs associated with monitoring the fires’ progression are moderate and typically may include temperature observation wells, thermal imaging (aerial), etc.
Surface Trenching Application
Surface trench application involves excavating an open trench in the unburnt coal seam ahead of the fire and removing the fuel (coal). This method decreases the available fuel for the fire. The fire is then left to burn until it is extinguished by lack of fuel.
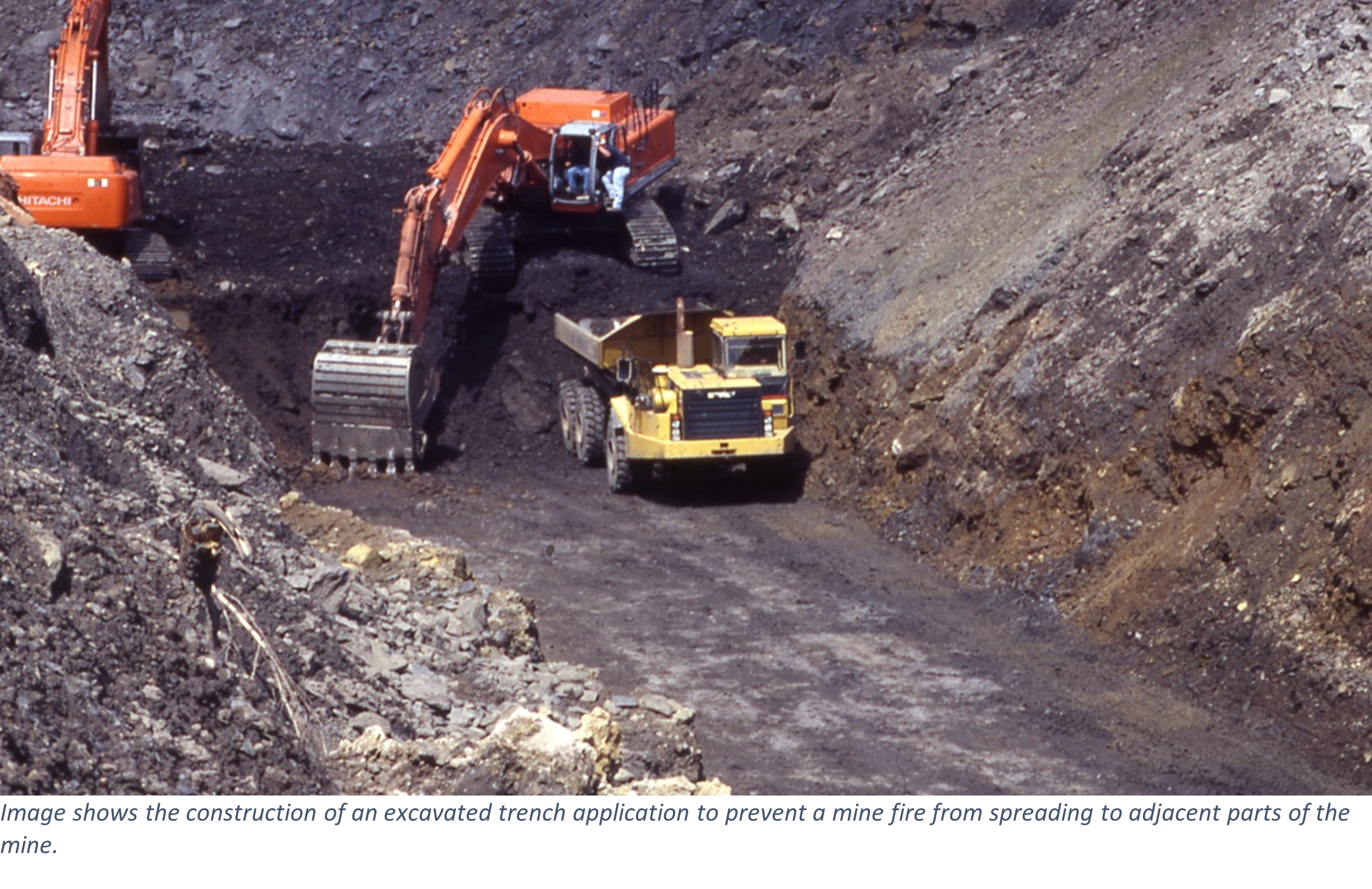
Environmental Impact: There is a relatively low environmental impact which mainly encompasses the trench construction zone.
Relative Costs: Excavation/blasting costs can be quite expensive. Due to the expense, this application is more practical for shallow smaller underground mine-fires. This application may also be used in conjunction with other firefighting applications.
Worker Safety: There is a minor risk to workers if the trench is located away from the fire area. If mine-fire gasses are present, personal protective equipment (PPE) will likely be required.
Public Safety: Public safety risks are significantly reduced outside the fire area and trench locations. Site security may be required to keep spectators and trespassers out.
Depth of Fire: Application is generally for small scale mine fires (several acres) with overburdens approximately 70 feet or less.
Multiple Burning Seams: This application is generally not used on multiple seam fires.
Available Technology: Standard excavation technologies.
Treatment Time: Highly dependent upon
Structural Geology: Not a concern.
Gasses, Smoke, and Soot: The risk of gasses, smoke and soot is high due to the lack of intervention.
Treatment by-products: None.
Maintenance and Monitoring Costs: Monitoring costs are minimal to moderate, and the frequency should increase as the fire reaches the trench to ensure the effectiveness of the trench.
Impassable Barriers Application
There are two main applications associated with this technique. In each case, an attempt is made to create a physical non-burnable barrier between the fire and fuel source.
- Injected Barrier Wall
- Cut off wall
Grout or Foam Barrier Walls Application
This application fills mine voids and bedrock fracturing above the coal with grout or foam to create a vertical non-combustible barrier which will slow the fire progression or prevent it from passing.
Analysis of “Injected Barrier Application:”
Overall Effectiveness: Very effective if the excavated trench encompasses the fire area. Ineffective in areas where trenching cannot be completed.
Environmental Impact: There is a relatively low environmental impact which mainly encompasses the trench construction zone.
Relative Costs: Excavation/blasting costs can be quite expensive. Due to the expense, this application is more practical for shallow smaller underground mine-fires. This application may also be used in conjunction with other firefighting applications.
Worker Safety: There is a minor risk to workers if the trench is located away from the fire area. If mine-fire gasses are present, personal protective equipment (PPE) will likely be required.
Public Safety: Public safety risks are significantly reduced outside the fire area and trench locations. Site security may be required to keep spectators and trespassers out.
Depth of Fire: Application is generally for small scale mine fires (several acres) with overburdens approximately 70 feet or less.
Multiple Burning Seams: This application is generally not used on multiple seam fires.
Available Technology: Standard excavation technologies.
Treatment Time: Highly dependent upon
Structural Geology: Not a concern.
Gasses, Smoke, and Soot: The risk of gasses, smoke and soot is high due to the lack of intervention.
Treatment by-products: None.
Maintenance and Monitoring Costs: Monitoring costs are minimal to moderate, and the frequency should increase as the fire reaches the trench to ensure the effectiveness of the trench.
Advantages
• Method is less expensive than trenching.
• Fewer safety hazards if barrier is placed outside of the fire zone.
• Can address fires deeper in depth than trenching would allow.
Disadvantages
• The total effectiveness of the barrier cannot be verified from the surface, the likelihood of preventing the fire from passing is low. Grout and foam cannot seal off unmined coal seams, therefore if there is a thin coal seam or parting in the location of the barrier, this would allow fuel for the fire to pass.
• As with trenching, it is necessary to be a distance from the fire to safely allow crews to work without the heat, smoke, and gasses.
• The most effective use of grout or foam barriers is to reduce the immediate advance of the fire giving time to engineers to develop other methods.
Cutoff Wall Application
Cutoff walls are designed to remove all overburden materials to the desired depth of the fire. The trench created is then backfilled with a non-combustible material isolating the fire from further advancement.
Analysis of “Cut-Off Wall Application:”
Overall Effectiveness: This application is highly effective. The reason for the effectiveness is because the entire overburden is removed eliminating the chance of the fire to pass beyond the trench through thin coal seams or poor-quality coal left from the mining.
Environmental Impact: There is moderate environmental impact which mainly encompasses the cut-off wall construction zone and access roads. Gasses and soot may be a present depending on the distance the barrier is from the fire.
Design Considerations: Due to the size of the equipment and the potential depth of the trench, subsurface ground stabilization may be needed to ensure the hydromill trenching bit does not drift.
Fire Fighting Costs: Costs for this application are high to very high due to the depth to the coal seams, equipment supports on subsided ground, and lack of companies with this type of equipment.
Worker Safety: There is a minor risk to workers if the wall is located away from the fire area. If mine-fire gasses are present, personal protective equipment (PPE) and monitoring will likely be required.
Public Safety: Public safety risks are very low beyond the cut-off wall and fire area.
Depth of Fire: This application can be useful for mine fires which are deep below the ground surface.
Multiple Burning Seams: This method is very useful where multiple burning seams are present. One properly engineered trench would provide a barrier for all seams below.
Available Technology: This technology is the most recent of all the fire-fighting applications. Therefore, only a few larger construction companies have access to this equipment.
Treatment Time: Treatment time is high. The reason is because the equipment cuts a 3-foot wide by 10 feet long trench to the desired elevation. The cutting head is removed, and the trench is backfilled prior to the start of the next panel. Backfill material will settle requiring topping off the trench panels over time.
Structural Geology: This application can be effective within steeply dipping bedrock.
Treatment by-products: There should be no treatment by-products.
Maintenance and Monitoring Costs: Maintenance and monitoring costs are low to moderate because settlement within the trench panels would require more material. Monitoring would mainly consist of heat monitoring across the barrier to ensure effectiveness.
Encapsulation Concept
Like barrier walls, there are two standard applications with a host of different materials to do the job. The concept of fire encapsulation is to reduce or eliminate the oxygen pathways to the fire. This effectively starves the fire of oxygen thus decreasing the advancement potential or outright extinguishes the fire. The two basic applications are:
- Surface Seal
- Mine Entry Seal
Surface Seal Application
This application involves sealing all oxygen intakes and smoke, debris, and gasses vents horizontally over the ground surface within the fire area. Beside intake and exhaust vents, this application also considers open bedrock fractures, either natural or subsidence related. This application is typically used for larger mine fires to reduce expended gasses and smoke. This application can also be effective for preventing secondary fires caused by the mine fire. Examples would include grass, forest, and structural fires. The seals are typically composed of local soils, however, alternatives such as compressed air, chemical, and water-based foams have also been used.
Analysis of “Surface Seal Application:”
Overall Effectiveness: This application is effective in reducing the available oxygen to the fire but should not be expected to extinguish it. This application is chiefly used to decrease the advancement of the fire and to seal exhaust vents where public hazards exist.
Environmental Impact: There is moderate environmental impact especially on larger fires where injection points are numerous and spread across the surface horizontally.
Design Considerations: When engineering the seal, the use of thermal imagery can be a valuable indicator of exhaust vents. Intake vents are going to be more difficult to identify. Beehive smokers or dry ice can be used to create a cloud which may be drawn into larger intake vents.
Fire Fighting Costs: Costs for this application are typically lower than isolation costs. Mainly, much of this application deals with surface or near surface areas.
Worker Safety: There is a moderate to high risk to workers safety due to the proximity of the fire and the exhaust vents. Special monitoring and PPE are likely to be required.
Public Safety: Public safety risks are low because at a minimum the exhaust vents are sealed preventing smoke and gasses from entering dwellings or igniting secondary fires.
Depth of Fire: This application can be useful for mine fires which are deep below the ground surface.
Multiple Burning Seams: This method is useful where multiple burning seams are present.
Available Technology: This application uses standard technologies.
Treatment Time: Treatment time is low. Once intake and exhaust vents are identified, sealing them should be relatively quick.
Structural Geology: This application can be effective within steeply dipping bedrock.
Treatment by-products: There is the possibility of steam pressure buildups in exhaust vents where water-based foams are used.
Maintenance and Monitoring Costs: Maintenance and monitoring costs are relatively high. In order to keep an effective seal, new exhaust and intake vents should be routinely identified and sealed.
Mine Entry (Shaft, Drift, Portal Seals) Application
This application addresses the abandoned mine-entries. The theory is that if the mine entries are sealed, this will reduce the available oxygen to the fire and restrict and cause a build-up of the exhaust fumes, smoke, and debris which will further choke the fire.
Analysis of “Mine Entry Seal Application:”
Overall Effectiveness: Similar to surface seals, this application is effective in reducing the available oxygen to the fire but should not be expected to extinguish it.
Environmental Impact: There should be no additional impacts beyond the fire area itself.
Design Considerations: Thermal imaging coupled with mine maps should be thoroughly reviewed to identify openings, shafts, or air intakes. Locations of mine seals may also be important when determining entries to seal.
Fire Fighting Costs: Costs for this application are typically low. Excavations may be necessary to ensure an effective seal.
Worker Safety: There is a low to moderate risk to workers due to the proximity of exhaust vents. Special monitoring and PPE are likely to be required.
Public Safety: Public safety risks are low to moderate because once the entries are sealed, it is likely that exhaust fumes will find other pathways to reach the atmosphere. This may cause exhaust vents to open in basements or other occupied structures.
Depth of Fire: This application can be useful for mine fires which are deep below the ground surface.
Multiple Burning Seams: This method is useful where multiple burning seams are present.
Available Technology: This application uses standard technologies.
Treatment Time: Treatment time is low. Once intake and exhaust vents are identified, sealing them should be relatively quick.
Structural Geology: This application can be effective within steeply dipping bedrock.
Treatment by-products: There is the possibility of steam pressure buildups in entries which are heated due to exhaust vents and the use of water-based foams.
Maintenance and Monitoring Costs: Maintenance and monitoring costs are moderate.
Injection Concept
This concept involves firefighting at the location of the underground fire. Because of the fire dangers, this concept does not involve excavations or applications which place personnel in or near the fire. As the title of this concept specifies, the materials used to combat the fire are injected into the area of the fire. Applications associated with this concept include:
- Water Injection or Flooding
- Compressed Air, Chemical, or Water Based Foams and Grout or Mud Injections
- Cryogenics
Flooding or Injection of Water Application
This application floods the fire with water, effectively removing the heat and thus extinguishing the fire. To accomplish this, mine portals are opened or cleaned out to allow the water to flow into the mine. It may also be necessary to create a containment dam that allows the waters to rise in the mine.
Analysis of “Flooding or Water Injection Application:”
Overall Effectiveness: This application can be very effective.
Environmental Impact: High environmental impacts are possible and would be expected to be localized. As the water builds up within the fire area, the high temperatures will cause the water to become steam. This steam will pressurize if an open pathway of venting does not exist. This significantly increases the likelihood of mine blowouts, new vents, movement of mine gasses, and even surface steam eruptions.
Design Considerations: Consulting available mine mapping and local geology is critical when evaluating a mine fire for flooding.
Furthermore, down dip features like entries, mine seals, and reclaimed areas should be tested for stability associated with an increased hydraulic head pressure.
Design consideration is also necessary for the source of the water used. Where is water supply large enough for project requirements? How will the water be delivered to the site, tanker truck, gravity, pipeline, etc.?
Fire Fighting Costs: Costs for this application are typically low with most costs associated with mine entry opening and water delivery.
Worker Safety: There is a low risk to workers unless the mine fire is venting at the injection point. If venting, special monitoring and PPE are likely to be required.
Public Safety: Public safety risks are high because of pressurized steam releases, mine blowouts, and slope failures.
Depth of Fire: This application can be useful for mine fires which are deep below the ground surface.
Multiple Burning Seams: This method is not typically used where multiple burning seams are present.
Available Technology: This application uses basic technologies. More recent technologies such as inflatable dams could be used to enhance down dip seals preventing blowouts.
Treatment Time: Treatment time is low. Once the injection point is opened, water can be injected until the mine fire is submerged.
Structural Geology: This application requires the bedrock to be dipping toward the fire area. Furthermore, down dip features like entries, mine seals, and reclaimed areas should be tested for stability prior to an increased hydraulic head pressure.
Treatment by-products: There is the possibility of steam pressure buildups, slope failures and mine seal blowouts related to increased water pressures along outcrops and entries.
Maintenance and Monitoring Costs: Maintenance and monitoring costs are low and typically would involve the monitoring of the heat signatures.
Compressed Air, Chemical, or Water Based Foam and Grout or Mud Injections Applications
Like flooding with water, this application floods the mine fire by saturating it with expanding foams, effectively removing the heat, and preventing oxygen from reaching the fire. This is accomplished by drilling injection holes into the mine workings near the fire. The expanding foam is pumped through the injection well into the mined coal seam or void spaces next to the fire where it spreads out. Over time the foam will expand, filling the voids and begins to suffocate the fire.
Analysis of “Compressed Air, Chemical, or Water Based Foam and Grout/Mud Injections:”
Overall Effectiveness: This application can be very effective.
Environmental Impact: High environmental impacts are possible and would be expected to be localized. As the water builds up within the fire area, the high temperatures will cause the water to become steam. This steam will pressurize if an open pathway of venting does not exist. This significantly increases the likelihood of mine blowouts, new vents, movement of mine gasses, and even surface steam eruptions.
Design Considerations: Consulting available mine mapping and local geology is critical when evaluating a mine fire for flooding.
Furthermore, down dip features like entries, mine seals, and reclaimed areas should be tested for stability associated with an increased hydraulic head pressure.
Fire Fighting Costs: Costs for this application are typically low with most costs associated with mine entry opening and water delivery.
Worker Safety: There is a low risk to workers unless the mine fire is venting at the injection point. If venting, special monitoring and PPE are likely to be required.
Public Safety: Public safety risks are high because of pressurized steam releases, mine blowouts, and slope failures.
Depth of Fire: This application can be useful for mine fires which are deep below the ground surface.
Multiple Burning Seams: This method is not typically used where multiple burning seams are present.
Available Technology: This application uses basic technologies. More recent technologies such as inflatable dams could be used to enhance down dip seals preventing blowouts.
Treatment Time: Treatment time is low. Once the injection point is opened, water can be injected until the mine fire is submerged.
Structural Geology: This application requires the bedrock to be dipping toward the fire area. Furthermore, down dip features like entries, mine seals, and reclaimed areas should be tested for stability prior to an increased hydraulic head pressure.
Treatment by-products: There is the possibility of steam pressure buildups, slope failures and mine seal blowouts related to increased water pressures along outcrops and entries.
Maintenance and Monitoring Costs: Maintenance and monitoring costs are low and typically would involve the monitoring of the heat signatures.
Cryogenics Application
The cryogenics application injects a combination of liquid carbon dioxide and nitrogen into the fire area. The concept is that the super cold gasses will remove the heat from the fire, effectively extinguishing it.
Analysis of “Cryogenics Application:”
Overall Effectiveness: This application is very effective when used as a fire-fighting suppression system in an active mine or in a small-scale fire. The effectiveness decreases as the fire size increases.
Environmental Impact: The main gasses used in firefighting consist of liquid carbon dioxide and liquified nitrogen. It is unknown how these heated gasses would affect the environment associated with large scale fires.
Design Considerations: As with all injection designs, available mine maps should be reviewed in conjunction with the fire data to determine the best injection points
Fire Fighting Costs: Costs for this application are high to very high with most costs associated with delivery and injection of cryogenic gasses.
A risk of asphyxiant is present at injection sites where carbon dioxide may displace oxygen in localized areas, even within an outdoor setting.
Worker Safety: There is a moderate risk to workers due to potential asphyxiant hazard and working with super cold materials. Special monitoring and PPE are likely to be required.
Public Safety: Risk levels associated with this application are unknown of a large-scale basis. Risk of large quantities of heated carbon dioxide entering adjacent structures may create a potential asphyxiant hazard. Oxygen or carbon dioxide monitoring would be recommended in these scenarios.
Depth of Fire: This application might be useful for mine fires which are deep below the ground surface.
Multiple Burning Seams: This method is not typically used where multiple burning seams are present.
Available Technology: This application uses more modern technologies. With the lack of use on largescale mine fires, it is unknown if other technologies would be necessary.
Treatment Time: Treatment time is presumed to be low.
Structural Geology: Bedrock dip would have an effect of the application of the gasses.
Treatment by-products: Byproducts of this application are unknown.
Maintenance and Monitoring Costs: Maintenance and monitoring costs are low to moderate and typically would involve the monitoring of the heat signatures.
Burning Refuse Piles
This type of mine fire occurs on coal waste piles. The fire ignites and burns on the coal fragments within the pile. The firefighting applications follow the same concepts as underground mine-fires, isolation, encapsulation, and injections. The method and materials used varies based on site characteristics.
It is also important to note that there is a high possibility of waste pile fires igniting underground mine-fires. Underground mine fires can start when the burning waste pile overlies a any coal seam.
Due to the proximity of the personnel and equipment to the fire, extreme safety measures need to be adhered to.
Excavations (dry versus wet)
The dry application involves the excavation and spreading of the waste pile in shallow lifts to allow for air cooling. In most cases, additional material is added to help cool it.
In the wet application, excavated material is doused with water or foam to begin the cooling process. After the addition of the water or foam, the rest of the treatment is the same as the dry application.
Analysis of “Excavation Application:”
Overall Effectiveness: This application is very effective and deals with the fire directly. However, it is useful on smaller fires only.
Environmental Impact: Impacts are negligible as only areas affected are abandoned spoil piles.
Design Considerations: Though no special design considerations are necessary for the excavation of the burning pile, much consideration is necessary for the source of the water used. Where is water supply large enough project requirements? How will the water be delivered to the site, tanker truck, gravity, pipeline, etc.?
Fire Fighting Costs: Excavations are costly and increase as the size of the fire increases.
Worker Safety: There are high risks to workers safety when excavating burning materials. Controls need to be in place to cool equipment and protect workers from gasses, smoke, and soot. When excavating refuse piles without a cooling aid, fire flare-ups are common as heated materials meet the atmosphere. Protection of the workers can take several forms, typically, enclosed cabs with air conditioning to protect from the heat and reduced times frames the equipment is exposed to the heat.
Public Safety: Unlike underground mine fires, public risks decrease as the fire is excavated.
Depth of Fire: This application is useful only on spoil piles which can be excavated through conventional means.
Available Technology: This application uses conventional technologies.
Treatment Time: Treatment time is dependent of the speed of excavation and size of the fire.
Treatment by-products: None.
Maintenance and Monitoring Costs: Maintenance and monitoring costs are low and typically consist of heat monitoring and thermal imaging.
Surface Seal Application
Like the surface seal application for underground mine fires, this application covers the waste pile with non-combustible material (usually soil) to prevent the flow of oxygen, to attempt suffocating the fire.
Analysis of “Surface Seal Application:”
Overall Effectiveness: This application is more effective for burning coal piles than underground fires.
Environmental Impact: Impacts are negligible as only areas affected are abandoned spoil piles.
Design Considerations: No special design considerations other than identification of the fire area.
Fire Fighting Costs: This application can be costly. The use of earthmoving equipment is expensive enough but adding fill material which will likely need transported to the site adds an additional cost.
Worker Safety: There is a moderate risk to worker safety and mainly involves working on heated earth and gasses and smoke. Necessary PPE will likely be required.
Public Safety: Public safety risk will lessen as the seal is constructed. At a minimum, smoke and gasses will be diverted to other exhaust vents away from residences.
Depth of Fire: This application is theoretically useful only on any size spoil pile. The larger the pile the higher the costs.
Available Technology: This application uses conventional technologies.
Treatment Time: Treatment time would be much faster than excavating the fire directly. The reason is that only the surface is treated instead of the entire burning zone.
Treatment by-products: None.
Maintenance and Monitoring Costs: Maintenance and monitoring costs are low and typically consist of heat and gas monitoring and thermal imaging.
Grouting or Injected Foam Application
This application calls for grout or foam to be injected into the waste pile to saturate voids with non-combustible materials. This saturation is two-fold, removing the oxygen from the fire and preventing it from moving to adjacent fuel sources.
Analysis of “Injection Application:”
Overall Effectiveness: This application is more effective for burning coal piles than underground fires. The main reason for this is that the void spaces between the spoil pile is greater than fracturing in bedrock. This allows the injected material to move through the spoil creating a better seal.
Environmental Impact: Impacts are negligible as only areas affected are abandoned spoil piles.
Design Considerations: No special design considerations other than identification of the fire area.
Fire Fighting Costs: This application is much more cost effective than excavation. This application is also more useful on larger fires.
Worker Safety: There is a moderate risk to worker safety and mainly involves working on heated earth and gasses and smoke. Necessary PPE will likely be required.
Public Safety: Public safety risk will lessen as the injections are constructed. At a minimum, smoke and gasses will be diverted to other exhaust vents away from residences.
Depth of Fire: This application is much more effective on deep fires.
Available Technology: This application uses conventional technologies.
Treatment Time: Treatment time would be much faster than excavating the fire directly. The reason is that using a semi-flowable injection material allows more coverage per injection point thus reducing the time needed for construction.
Treatment by-products: None.
Maintenance and Monitoring Costs: Maintenance and monitoring costs are low and typically consist of heat and gas monitoring and thermal imaging.